Proven Roof Coating Maintenance Strategies
At Pepper Coatings, we’ve spent over 20 years helping property owners protect their investments through high-performance roof coating solutions designed specifically for North Texas weather conditions. Our experience has taught us that while quality application is essential, proper maintenance is equally critical to maximizing the lifespan and effectiveness of any roof coating system. What sets our approach apart is our comprehensive understanding of how DFW’s unique climate challenges—from blistering summer heat to severe hailstorms—affect different coating types and roofing substrates. We don’t just apply coatings; we partner with our clients to ensure their roof protection systems deliver maximum value through proper maintenance and timely service. Our team of certified roof coating specialists combines technical expertise with a commitment to transparent communication, ensuring you understand exactly what your roof needs and why. This educational approach has earned us a reputation as DFW’s most trusted roof coating resource, with over 75% of our new business coming from client referrals and a 97% customer satisfaction rating.
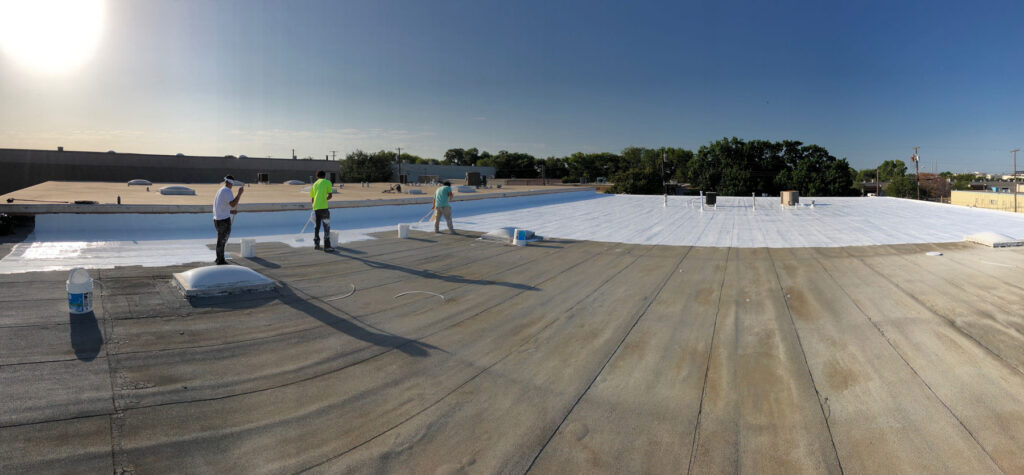
Understanding Your Roof Coating’s Vulnerabilities in North Texas
The first step in effective maintenance is recognizing what threatens your roof coating’s integrity:
DFW-Specific Climate Challenges
North Texas weather creates unique stresses on roof coating systems:
Extreme temperature fluctuations are particularly damaging to roof coatings. During summer months, surface temperatures on Dallas-Fort Worth roofs can exceed 160°F, while winter can bring freezing conditions. This expansion and contraction cycle stresses coating adhesion and can lead to premature cracking if not properly maintained.
UV exposure in DFW is significantly higher than the national average, with approximately 234 sunny days annually compared to the U.S. average of 205. This intense sun exposure accelerates coating degradation through photodegradation—the breakdown of polymers by ultraviolet light. Regular maintenance helps identify early signs of UV damage before they compromise the coating’s protective properties.
Severe weather events including hailstorms, thunderstorms, and occasional tornadoes can cause impact damage, punctures, and accelerated wear. The Dallas-Fort Worth metroplex experiences an average of 40 severe weather days annually, making damage inspection after significant storms an essential maintenance practice.
Common Early Warning Signs
Knowing what to look for can prevent minor issues from becoming major problems:
Surface chalking, where a powdery residue forms on the coating surface, is often the first visible sign of degradation. While some chalking is normal as coatings weather, excessive chalking indicates accelerated breakdown and should prompt a professional evaluation.
Blistering or bubbling in the coating surface typically indicates moisture trapped beneath the coating or adhesion failure. These issues are particularly common on flat or low-slope roofs throughout Arlington, Irving, and eastern Fort Worth areas where water pooling is more common.
Cracking or alligatoring (a pattern of interconnected cracks resembling alligator skin) signals that the coating has lost elasticity, often due to excessive UV exposure or age. This condition requires immediate attention as it compromises the waterproofing integrity of the entire system.
Professional vs. DIY Maintenance: What Property Owners Should Handle
Understanding which maintenance tasks require professional expertise helps optimize your maintenance budget:
Safe DIY Maintenance Tasks
Property owners can safely handle several important maintenance functions:
Visual inspections from the ground using binoculars can identify obvious issues like major debris accumulation, displaced gravel (on coated ballasted systems), or visible damage after storms. This regular monitoring helps catch problems early without requiring roof access.
Gutter and downspout cleaning at ground level reduces the risk of water backing up onto the roof surface. Ensuring proper drainage away from the foundation also protects the structure beneath your coated roof.
Documentation of changes, weather events, or visible concerns creates a valuable history for professional maintenance providers. Dated photographs of your roof after significant weather events are particularly helpful for tracking progressive changes or documenting insurance claims when necessary.
When to Call the Professionals
Certain maintenance aspects require specialized equipment and expertise:
Adhesion testing to verify continued bonding between the coating and substrate requires professional equipment and interpretation. This preventative measure can identify potential adhesion failures before they lead to larger problems.
Reflectivity measurements using specialized tools provide objective data about coating performance degradation. For buildings in high-density areas like downtown Dallas, Las Colinas, or Frisco business districts, maintaining optimal reflectivity can significantly impact cooling costs during DFW’s extended summer season.
Coating thickness evaluation ensures adequate protection remains across the entire roof surface. Coatings naturally erode over time, with rates varying based on exposure, slope, and local conditions. Professional measurement identifies areas requiring reapplication before waterproofing is compromised.
Protect Your Roof Coating Investment with Expert Care
Your roof coating represents a significant investment in your property’s protection and energy efficiency. With proper maintenance, quality roof coatings in the DFW area can provide 10-15 years of reliable service, even under our challenging climate conditions.
Contact Pepper Coatings today to schedule your comprehensive roof coating inspection and maintenance assessment. Our DFW-based specialists will evaluate your current coating condition, identify any maintenance needs, and provide a clear plan to maximize your roof coating’s lifespan and performance. Don’t wait until problems are visible—preventative maintenance is the key to long-term protection and value.